Together with the charging machines, OTTO JUNKER supplies the entire equipment from a single source. The furnaces are normally arranged in parallel so that the handling equipment can be used for several furnaces.
Design and concept are made to match the customers’s individual requirements with regard to space, layout, take-over and hand-over points. OTTO JUNKER charging machines also offer the opportunity of arranging the furnaces opposite each other so that the charging machine can charge the hot furnaces at both ends.
The furnaces can be either gas-fired or electrically heated, with electric heating offering the possibility of CO2 free operation. Gas-fired furnaces use self-recuperative high velocity burners with maximum efficiency.
The heat treatment process is typically conducted in a protective gas atmosphere to prevent discolorations due to the rolling oil / emulsion sticking to the strip. For special applications / alloys, the cooling inside the furnace can also be carried out under a protective gas atmosphere. However, it can also be carried out purely under air atmosphere with an air purging system.
The purging gas or purging air can be preheated by means of the optional OTTO JUNKER energy recovery system.
The intense recirculation by means of high convection ensures a high heating rate and homogeneous temperature distribution, free from streaks and without local overheating. Press-on thermocouples serve to monitor the heating-up process of the coils.
Cooling of the coils takes place outside of the furnace under air. The cooling process can be speeded up by means of separate cooling spots or cooling chambers. If necessary, cooling can also take place under protective gas atmosphere inside the furnace proper, using a high-performance cooling system.
Strip coil furnaces are frequently designed as multi-coil furnaces. For single coil furnaces, feeding by means of scissor-type lifting table offers particular space advantages (elevator furnace).
Benefits at a glance:
- Short heating and cooling times
- High throughput
- Temperature uniformity conforming to CQI9 and AMS specifications
- Low energy demand
- Model-based furnace control system to minimize cycle times
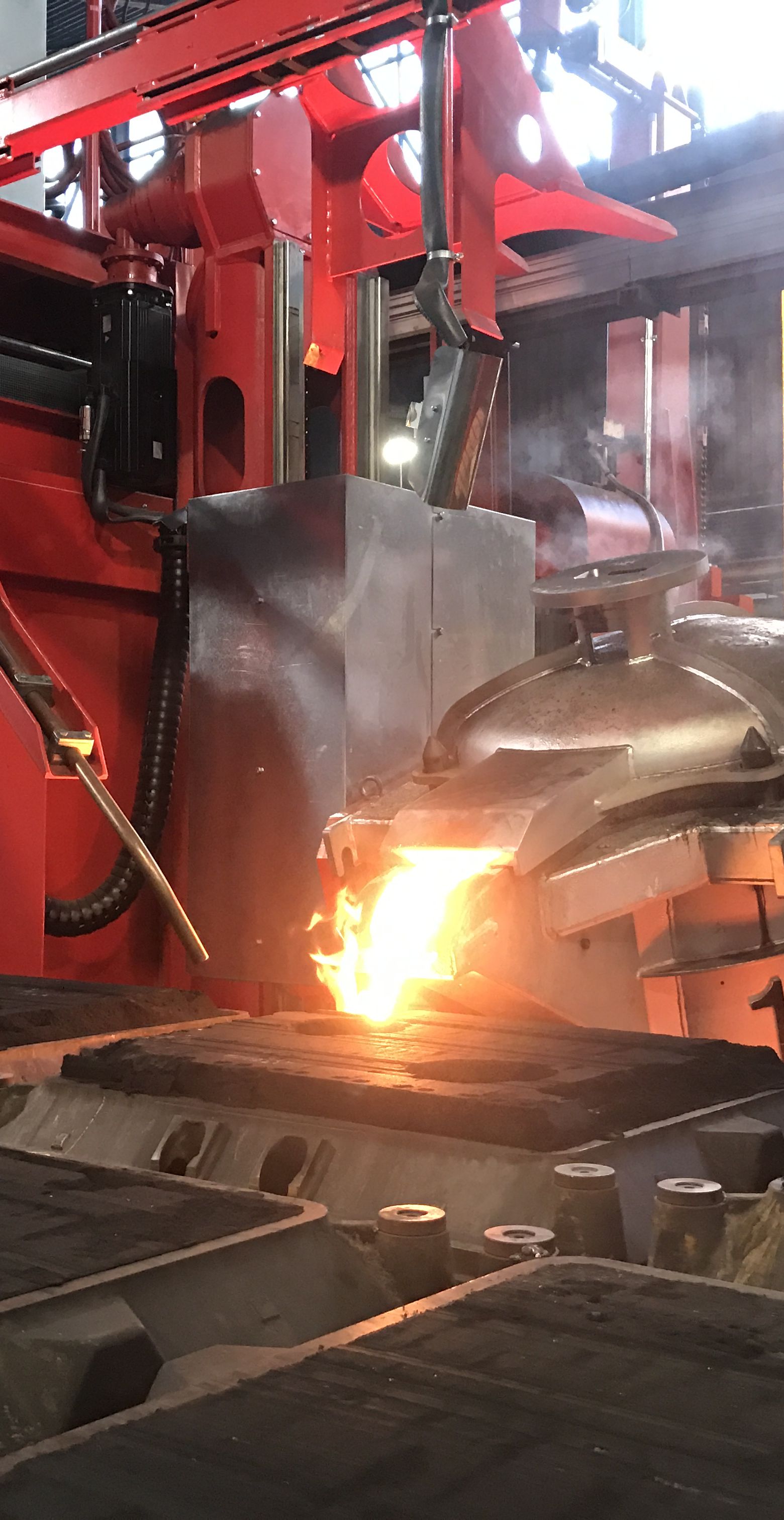
Automation and visualization
Reliability and ease of operation are essential for high product quality at maximum throughputs. Schematic images in the visualization provide information about the production process and the function of system components at any time. Process data are continuously recorded for quality monitoring. An integration into higher-level IT systems (Level 3) is possible.
Mathematical model / Digital Twin
Mathematical model for optimization of your furnace plant.
■ Shorter cycle times through quicker coil call-off
■ Continuous reduction of costs and resources due to efficient use of energy
The integrated process model calculates the temperature in the coil while the traditional press-on thermocouples can only detect the start temperature of the coil. Due to the known temperature distribution, the model helps to make full use of the temperature overshoot, thus reducing the heating-up time.
The model allows an improved power control increasing process repeatability. Press-on thermocouples on the charging machine detect the start temperature of the coil. Different start temperatures of the coils within one batch are automatically levelled by means of the mathematical model.
Press-on thermocouples in the furnace can serve as an additional safety feature and for a continuous comparison with the process model.
The integrated process model ideally complements the heating process. By calculating the temperature curve in real time, heat input is applied in the best possible way and the heating-up time is reduced.
OTTO JUNKER can also offer you to retrofit a process model for your existing equipment individually tailored for your production. We supply the required hardware and software and integrate the model into your existing control software.
Installation on site
Detailed planning and execution of the complete equipment installation by our specialists on site ensure a workmanlike and timely installation.
Our services include:
- Supervision of installation
- Commissioning of the equipment
- Delegation of installation personnel with tools, hoisting gear, etc.
Advantages:
- Everything from a single source
- Timely and workmanlike installation
- Professional site management
- Start of production with Junker personnel on stand-by
- Long service life
Technology Centre
Basic investigations can be carried out on test facilities for heating and cooling in the OTTO JUNKER Technology Centre. Apart from process observations, flow and thermal investigations can be performed.
If necessary, the facilities can be adjusted to your individual questions.
Strip width | max. 2,500 mm |
Coil diameter | max. 2,600 mm |
Coil weight | max. 30 t |
Batch size | 1 to 8 strip coils |
Downloads
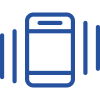
Phone +49 2473 601-0
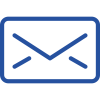
E-Mail sales@otto-junker.com