Energiesparen beim Schmelzen in Induktionsöfen
- 24. September 2024
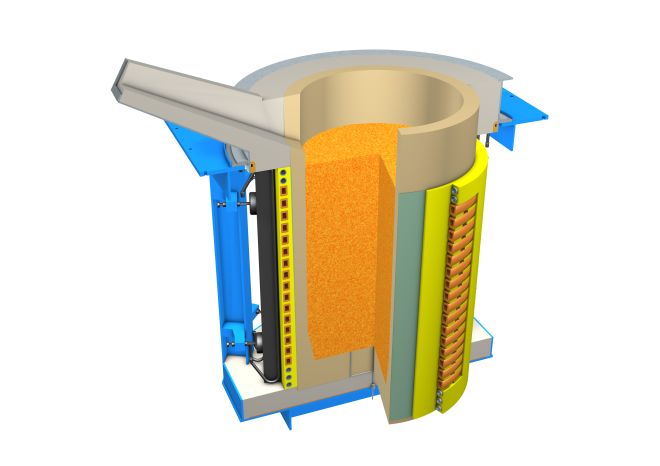
Frank Donsbach, Matias Mohedano Rodriguez, Ulrich Nordt – OTTO JUNKER GmbH, D-52152 Simmerath-Lammersdorf, und Peter Koldig Hansen, Init Inuatek A/S, DK-1432 Kobenhaven K
Induktionsöfen sind hervorragend geeignete Aggregate zum CO2-neutralen Schmelzen sämtlicher Metalle. Führt man den Induktionsofen als Tiegelofen (s. Bild 1) aus, so befindet sich im Inneren einer zylindrischen Kupferspule ein keramischer Tiegel. Das Schmelzgut welches man in diesen Tiegel gibt, wird durch Stromfluss durch die Kupferspule einem elektromagnetischen Feld ausgesetzt. Dieses Feld induziert Wirbelströme in das metallische Schmelzgut. Die ohmschen Verluste dieser Wirbelströme erwärmen das Schmelzgut und verflüssigen es letztendlich.
Solche Induktionstiegelöfen erzielen bei hochleitfähiger Ausführung des Spulenkupfers und streuarmer Rückführung des elektromagnetischen Feldes durch Joche aus Transformatorenblech Wirkungsgrade von über 80 % für Eisenwerkstoffe und über 70 % für gutleitfähige Werkstoffe wie Kupfer oder Aluminium.
[Bild 1: 3D-Grafik eines Tiegelofens]
Alternativ lässt sich ein Induktionsofen auch nach dem Rinnenofenprinzip bauen (s. Bild 2). In diesem Fall flanscht man einen sogenannten Rinneninduktor (oder mehrere davon) (s. Bild 3) an ein Oberofengefäß an. Die Erwärmung der flüssigen Schmelze erfolgt nach dem Prinzip eines kurzgeschlossenen Transformators. Dabei bildet eine Kupferspule die Primärwicklung und ein Kanal aus flüssigem Metall die kurzgeschlossenen Sekundärwicklung. In diesem Kanal fließt dann der Kurzschlussstrom des Transformators, seine ohmschen Verluste wiederum erhitzen das Metall. Dieses elektrotechnische Prinzip erreicht sogar noch 10-20 %-Punkte höhere Wirkungsgrade als das Tiegelofenprinzip. Es weist jedoch die Nachteile auf, dass eine Totalentleerung des Ofens vermieden werden muss und somit Einschränkungen hinsichtlich der Legierungs- und Betriebsflexibilität bestehen.
[Bild 2 : Induktionsofen in Trommelform zum Schmelzen von OF-Kupfer entsprechend des Rinnenofenprinzips]
[Bild 3: 3D Grafik eines W-Rinneninduktors]
Der Tiegelofen weist außerdem den Vorteil auf, dass sich wesentlich höhere Leistungen realisieren lassen. So sind Tiegelöfen für Eisen und Stahl mit mehr als 20 MW und Schmelzleistungen von mehr als 40t/h erfolgreich im Einsatz.
Auch wenn der Induktionsofen mit Strom aus erneuerbaren Energien CO2 frei betrieben werden kann, so sind die anwendenden Gießereien bestrebt, die Öfen mit einem möglichst geringen Stromverbrauch zu fahren. Dies erfolgt aus Gründen der nachhaltigen Ressourcenschonung und auch der Wirtschaftlichkeit von Gießereien und Halbzeugwerken, insbesondere bei steigenden Energiekosten. Die Verflüssigung von Eisenwerkstoffen oder Aluminiumwerkstoffen benötigt ca. 500-560 kWh/t, somit werden die Energiekosten häufig zu einem wesentlichen Faktor der Guss- und Halbzeugherstellung.
Welche Möglichkeiten hat nun der Gießer um Energie beim Schmelzen einzusparen? Im Wesentlichen gibt es drei Einflussfaktoren:
- Dimensionierung der Anlage und Gestaltung des Stromliefervertrages
- Praktische Fahrweise der Schmelzöfen
- Auswertung digitaler Schmelzprozessdaten
Dimensionierung der Anlage und Gestaltung des Stromliefervertrages
Heutige Stromlieferverträge weisen meist einen Leistungspreis, einen Arbeitspreis und einen Blindstrompreis aus. Die mit dem Leistungspreis verbundenen Kosten lassen sich dadurch senken, dass die Anlage möglichst gleichmäßig Energie aus dem Netzt bezieht. Der Energieversorger lässt sich den Bezug von Leistungsspitzen, die er von der Erzeuger- und Stromnetzseite bereitstellen muss, entsprechend bezahlen. Es macht also Sinn, eine Schmelzofenanlage so zu dimensionieren, dass der geplante Flüssigmetallbedarf gedeckt wird, der temporäre Maximalbedarf jedoch - falls möglich - durch zusätzliche Produktionszeiten erreicht wird. Hilfreich sind hierbei auch Maximumüberwachungsanlagen, die dafür sorgen, dass vorher definierte Verbraucher bei Erreichen der Grenzleistung gedrosselt werden. Einen Vorteil für diese Betriebsweise bieten Induktionsofenanlagen mit pulsweitenmodulierten IGBT Umrichtern, weil diese auch im Teillastbereich einen konstanten Leistungsfaktor cos phi aufweisen, bei dennoch sehr gutem elektrischen Wirkungsgrad des Parallelschwingkreisumrichters. Einen konstanten Netzleistungsfaktor erreichen auch Serienschwingkreisumrichter. Bei diesen muss jedoch der hohe unkompensierte Ofenstrom durch den gesamten Wechselrichter geführt werden, was zu zusätzlichen Verlusten und höherer Bauteilbelastung führt.
Der Arbeitspreis im Stromliefervertrag bestimmt die Kosten pro verbrauchter kWh, die vom Schmelzbetrieb zu zahlen sind. Beträgt dieser z.B. 20 Cent pro kWh und die Ofenanlage verbraucht 550 kWh/t Flüssigmetall, so lägen die elektrischen Arbeitspreiskosten pro Tonne Guss oder Halbzeug bei 110 Euro.
In einigen Netzen kann es auch sein, dass in Abhängigkeit von Tageszeit oder Wochentag die Arbeitspreiskosten unterschiedlich sind. In solchen Fällen kann die Installation eines Warmhalteofens oder einer Ofenanlage mit zwei oder drei Tiegeln zum Speichern flüssiger Schmelze, die in der Niedrigtarifphase erzeugt wurde, sinnvoll sein.
Ob zusätzlich noch Kosten für die verbrauchte Blindleistung zu zahlen sind, hängt zum einen davon ab, welcher Blindleistungsverbrauch vom Energieversorger zugelassen wird und zum anderen davon, ob die Induktionsofenanlage auch im Teillastbereich einen konstanten cos phi von z.B. 0,99 am Umrichtereingang aufweist.
Sollte der Arbeitspreis keinen Niedrigtarif aufweisen und der Flüssigmetallbedarf relativ kontinuierlich sein, so empfiehlt es sich möglichst auf die Installation von zusätzlichen Warmhalteöfen zu verzichten. Beispielsweise hat ein 60 Tonnen Warmhalteofen für Eisen, ausgeführt als Rinneninduktionsofen, einen Jahresenergiebedarf von ca. 2 Mio. kWh. Gemäß dem Beispiel mit 20 Cent pro kWh, betragen die Energiekosten also 400.000 Euro pro Jahr.
Praktische Fahrweise der Schmelzöfen
Wie auch beim Autofahren kann beim Betrieb eines Induktionsschmelzofens ein nennenswerter Anteil des Energiebedarfs allein durch eine geschickte Fahrweise eingespart werden. Dies beginnt bereits bei der Auswahl und Weiterverarbeitung des Einsatzmaterials.
Somit lassen sich die Sparmaßnahmen in zwei Kategorein unterteilen: Optimierung der Art und Qualität des Einsatzmaterials und Optimierung des Prozessablaufs.
Häufig wird Verunreinigungen an den Oberflächliche keine besondere Aufmerksamkeit geschenkt, da sich rein optisch kein Unterschied festmachen lässt. Das Material schmilzt augenscheinlich ebenso gut ein wie reines Metall. Nach dem Schmelzvorgang werden die nichtmetallischen Verunreinigungen in Form von Schlacke abgetragen.
Fakt ist jedoch, dass diese Verunreinigungsanteile insgesamt eine schlechtere Ankopplung der Schrotte an das Magnet / oder Induktionsfeld bewirken. Im Falle von Oxiden koppeln diese sogar gar nicht erst an, was insgesamt zu einer schlechteren Leistungsausnutzung führt.
In der Praxis ergeben sich solche Erkenntnisse meist erst durch Auswertung der Produktionsdaten. Werden Unregelmäßigkeiten im Prozess oder in der Produktqualität festgestellt, entsteht der Handlungsbedarf und der Prozess wird systematisch untersucht.
Im Folgenden einige exemplarische Prozesssituationen und zugehörige Orientierungswerte für Einsparpotentiale hinsichtlich des Energiebedarfs bei Einschmelzen einer Charge, wie sie in unterschiedlichen Eisengießereien ermittelt wurden.
1 Sand im Einsatzmaterial
Nach dem Abrütteln der Formen bleiben mal mehr, mal weniger Reste von Formsand am Kreislaufmaterial haften. Wenn diese nicht hinreichend abgestrahlt werden, gelangt somit Sand in die Schmelze. Auch für die Bildung von Schlacke aus dem Sand wird Energie benötigt. Bei einer realistischen Menge von 25 kg Sand pro Tonne Eisen, ergibt sich ein erhöhter Bedarf von 25 kWh/t.
2 Verrostetes Einsatzmaterial
Je nach Lagerbedingungen der eingesetzten Schrotte können diese Rost (Eisenoxide) in den Schmelztiegel einbringen. Die schlechte Ankopplung führt zu einer geringeren Leistungsaufnahme. Das Eisenoxid muss energieintensiv auf die Schmelzetemperatur erhitzt werden. Für den Beispielofen aus der Tabelle (s. Bild 4) bedeutet dies einen Mehrverbrauch von 30 kWh/t.
3 Niedrige Packungsdichte
Auch die Packungsdichte des Einsatzmaterials beeinflusst den Energieverbrauch: Je höher die Packungsdichte ist, desto niedriger ist der Energieverbrauch.
Messungen im praktischen Betrieb zeigten eine Verlängerung des Schmelzvorgangs um ca. 8 % und eine Erhöhung des Energiebedarfs um ca. 25 kWh/t bei einer Reduzierung der Packungsdichte von 2,0 t/m3 auf 1,3 t/m3.
4 Aufkohlen nach dem Einschmelzen
Wird das Aufkohlungsmittel nicht am Anfang des Schmelzvorganges und zusammen mit den metallischen Einsatzstoffen eingesetzt, sondern erst nach dem Aufschmelzen in das flüssige Bad eingebracht, ergibt sich ein deutlich höherer Energiebedarf. Anhand praktischer Erfahrungen ließ sich ermitteln, dass bei nachträglichem Einrühren ca. 1 bis 2 kWh/kg Kohlungsmittel zusätzlich erforderlich sind. Bei einem realistischen Wert von 1 % Aufkohlungsmittel je Charge, ist also ein höherer Energiebedarf von max. 5 bis 10 kWh/t Eisen zu erwarten.
5 Schmelzen mit reduzierter Leistungsdichte
Laut den theoretischen Überlegungen ist die Ofenfahrweise mit maximal verfügbarer elektrischen Leistung und damit hoher Leistungsdichte energetisch am günstigsten. Durchgeführte systematische Versuche bestätigen dies auch eindeutig. Die Chargenzeit wird verkürzt, die thermischen Verluste sinken und in der Folge wird der Stromverbrauch reduziert. Fährt man den Beispielofen aus der Tabelle unten mit nur 50 % der Maximalleistung ergibt sich ein Mehrverbrauch von 20 kWh/t.
6 Schmelzen mit Sumpf
Der Einsatz der Mittelfrequenztechnik ermöglicht das Schmelzen ohne Sumpfund das Einschmelzen von kleinstückigem Material. Aufgrund der besseren elektromagnetischen Ankopplung des festen Einsatzmaterials (gilt nur für Eisengusswerkstoffe) wird im reinen Chargenbetrieb 5 % weniger Energie benötigt, da bis zum Curiepunkt ein wesentlich höherer Spulenwirkungsgrad erreicht wird.
7 Warmhalten mit offenem Deckel
Wird ein Ofen länger als erforderlich mit offenem Deckel betrieben, entweicht ein erheblicher Anteil der Hitze in die Umgebung. Diese Energie muss nachgeführt werden. Der geringe thermische Verlust von ursprünglich etwa nur 275 kW (bei einem 15-Tonnen-Ofen) steigt dann auf etwa 600 kW an. Betrachtet man hier einen Zeitraum von 20 Minuten, ergibt sich ein erhöhter Energiebedarf von 15 kWh/t.
8 Ungedrosselte Absaugung
Die Absaugmenge der Abgasreinigungsanlage sollte den Prozessschritten des Ofens angepasst werden. Wenn keine Rauchgase abzuführen sind oder nur eine geringe Menge anfällt, kann die Absaugmenge gedrosselt werden.
Betreibt man die Filteranlage immer mit voller Leistung, wird unnötig Energie aus dem Ofen „abgesaugt". Der Mehrverbrauch kann in ungünstigen Fällen in einer Größenordnung von 2 % liegen. Im Beispiel der Tabelle wird dies mit 8 kWh/t beziffert.
9 Unnötiges Überhitzen
Wird in der letzten Phase des Aufschmelzens im Handbetrieb das Überhitzen des Eisens nicht rechtzeitig überprüft, kann es passieren, dass die gewünschte bzw. ausreichende Abgusstemperatur unnötig überschritten wird. Bei Vermeidung einer übermäßigen Temperaturerhöhung von 50 K, kann man hier ca. 20 kWh/t einsparen.
Bei Einsatz einer digitalen Ofensteuerung kann im Automatikbetrieb die Endtemperatur bis auf 5 K genau eingehalten werden. Damit wird eine unnötige Überhitzung vermieden.
In der Tabelle werden zur Veranschaulichung für einen Ofen mit einem Fassungsvermögen von 8.000 kg Gusseisen, betrieben mit einer Maximalleistung von 7.000 kW die zuvor aufgezählten Beispiele mit Energiewerten beziffert.
Natürlich kommen diese individuellen Fälle niemals alle gleichzeitig zusammen. Die Gesamtsumme zeigt jedoch, dass der benötigte Energiebedarf im schlimmsten Fall sogar um über 35 % überschritten werden könnte.
Legt man hier die anfangs angenommenen Stromkosten von 20 Cent pro kWh zu Grunde, verteuert sich die Herstellung von einer Tonne um 30 EUR. Bei einer Jahresproduktion von 50.000 Tonnen im Jahr bedeutet dies also insgesamt vermeidbare Mehrkosten von etwa 1.500.000 EUR.
[Bild 4: Energieeinbußen durch schlechtes Material und ungünstige Ofenfahrweise]
Da man sich der Ursachen bewusst ist, lässt sich sehr einfach durch Etablieren von routinierten Handlungen und einer optimierten Systematik eine Energieverschwendung unter Zuhilfenahme der Qualitätsüberwachung und Prozesssteuerung vermeiden.
Die gleiche Software die für die Bedienung des Ofens eingesetzt wird, kann um derart hilfreiche Bausteine erweitert werden, wie etwa Rezeptführung oder Prozessschritt-Bestätigung. Dabei können je nach Gießereiprozess und Schmelzaufgabe individuelle Ziele verfolgt werden.
Auswertung digitaler Schmelzprozessdaten
Moderne Induktionsofenanlagen verfügen über eine SPS Steuerung und einen Prozessrechner, der alle wichtigen Schmelzprozessdaten speichert und einer bestimmten Charge zuordnet. Eine vollständige Chargendokumentation enthält folgende Informationen/Daten (s. Bild 5):
[Bild 5: Beispiele für Daten aus einem Chargenbericht]
[Bild 6: Beispiel Schmelzparameter]
Optional können noch Daten wie Öffnungszeiten des Deckels, Zeiten starker und gedrosselter Absaugung, optimale oder verzögerte Materialzuführung, optimale oder verzögerte Materialabgabe erfasst werden.
Ein Chargendiagramm gibt einen Überblick über die Materialzuführung, Temperatur und Leistungsaufnahme aufgetragen über die Chargenzeit. Zum Vergleich kann optional eine „Idealcharge“ hinterlegt werden, welche der Bediener dann durch möglichst günstiges Chargieren zu erreichen anstreben kann. Für eine solche nach stetiger Verbesserung in Durchsatz und Energiebedarf strebende Fahrweise, empfiehlt es sich einen separaten Rechner mit eigenem übersichtlichen Dashboard zu installieren, um somit die Optimierung der Fahrweise von der Visualisierung der Ofenanlagensensorik zu separieren.
Dies gibt dem Ofenbediener eine transparente Echtzeitinformation, ob er den Ofen energiesparend gefahren hat. Dies hat auch eine motivierende Wirkung auf den Bediener, da er direkt den wirtschaftlichen Einfluss seiner Arbeitsweise oder den von verschieden Schrottqualitäten erkennen kann.
[Bild 7: Typische Darstellung des Hauptbildschirms einer modernen Ofensteuerung, hier: JUMI Junker Melting Interface]
Die Analyse dieser Schmelzprozessdaten kann darüber hinaus durch eine künstliche Intelligenz unterstützt werden um ggf. Muster „guter oder schlechter“ Chargenergebnisse in Abhängigkeit der zahlreichen Parameter zu finden und Optimierungsvorschläge für Chargiermaterialien und Ofenfahrweise zu erarbeiten.
Effizienzsteigerung durch datengesteuerte Praktiken
Im Bereich der Gießereien hängt der effiziente Betrieb von Schmelzöfen stark von „Streamlining“ durch Datenanalyse ab. Die erfolgreiche Umsetzung von Betriebsverfahren (SOPs) spielt eine entscheidende Rolle bei der Optimierung des Energieverbrauchs.
Erreichen idealer Schmelzprozesse:
Ein idealer Schmelzprozess ist durch eine kontinuierlich ansteigende kumulative Energieverbrauchskurve gekennzeichnet. Längere "flache Perioden" auf dieser Kurve deuten auf suboptimale Schmelzbedingungen hin. Aufgrund mangelnder Datentransparenz arbeiten die Schmelzöfen jedoch häufig auf der Grundlage individueller Erfahrungen der Bediener und subjektiver „Best Practices“. Die Herausforderung verschärft sich noch, wenn die Bediener mehrere Öfen in riesigen Werkshallen verwalten, was es schwierig macht, zeitnahe Erkenntnisse zu gewinnen.
Bediener-Nudging-Dashboards
Nehmen wir zum Beispiel eine große Gießerei in Nordeuropa, die jährlich 100 GWh verbraucht. Auf der Suche nach optimalen Bedingungen ergaben Untersuchungen, dass für das Schmelzen von einer Tonne Schrott bis zum flüssigen Eisen idealerweise etwa 560 kWh benötigt werden sollten. Der tatsächliche Durchschnitt lag jedoch bis vor kurzem bei 640 kWh pro Schmelze. Um dies zu ändern, arbeitete die Gießerei mit einem Unternehmen aus Dänemark zusammen, das IoT-basierte Energieoptimierungsdienste speziell für Gießereien anbietet.
Die Experten analysierten die Daten mehrerer Schmelzchargen, um die idealen Betriebsabläufe zu ermitteln, und organisierten die Informationen in Echtzeit-Dashboards für die Bediener. Diese Dashboards, die in den Fahrzeugen der Bediener angebracht sind (s. Bild 8 a und b), zeigen Temperatur, Energieverbrauch und Gewicht des Ofens an. Sie bieten auch eine klare visuelle Anleitung für den idealen Zeitpunkt zum Befüllen und Entleeren der Öfen. Durch diese Initiative konnte der durchschnittliche Energieverbrauch auf 570 kWh gesenkt werden, was allein für den Schmelzprozess eine jährliche Einsparung von fast 1 Million Euro bedeutet.
[Bild 8, a und b: Typische Anzeige des Nudging Dashboards im Stapler des Bedieners]
Erreichen einer Energiebilanz
Aufbauend auf diesen Erfahrungen integrierte die Eisengießerei vorhandene Ofendaten mit MES- und ERP-Systemen, um die Produktion auf Zeiten niedriger Energiepreise abzustimmen. Dies mag zwar wie eine Kostensenkungsstrategie erscheinen, dient aber auch dem umfassenderen Ziel, die Stabilität des Stromnetzes durch die verstärkte Nutzung erneuerbarer Energiequellen zu unterstützen.
Durch die strategische Anpassung der Leistung strombetriebener Anlagen für kurze Intervalle (5-15 Minuten) können Gießereien von den Übertragungsnetzbetreibern (ÜNB) hohe Erstattungen erhalten, indem sie in den Energieausgleich eintreten, ohne dass die Produktion wesentlich beeinträchtigt wird. Für Gießereien, die Induktionsöfen verwenden, ist dies eine großartige Gelegenheit, leicht verfügbare Daten von Öfen, MES- und ERP-Systemen zu nutzen, um Nachhaltigkeit, Effizienz und einen geringeren CO2-Fußabdruck zu erreichen.
Literaturverzeichnis:
- Trauzeddel, D. (2018) Spezielle Anwendungen der induktiven Schmelz- und Gießtechnik. Einsatzgebiete | Anlagenbau | Prozesstechnik. Vulkan Verlag.
- Dötsch, E. (2019) Induktives Schmelzen und Warmhalten. Grundlagen | Anlagenaufbau | Verfahrenstechnik. Vulkan Verlag.
- Donsbach, F.; Schmitz, W.; Trauzeddel D. (2018) OTTO JUNKER Handbuch: Sicheres und energiesparendes Schmelzen im MF-Tiegelofen. Selbstverlag.
- Donsbach, F.; Renftle, G.; Niklaus, S. (2021) Das Einschmelzen von Schrotten geringer Packungsdichte im Mittelfrequenz- Induktion-Tiegelofen. Fachartikel.
- OTTO JUNKER Akademie
- Fotos: OTTO JUNKER Archiv
- Fotos: INDUGA Archiv
- Init Group